Wafer dicing-tekniken, som ett kritiskt steg i halvledartillverkningsprocessen, är direkt kopplad till chipprestanda, utbyte och produktionskostnader.
#01 Bakgrund och betydelse av waferdicing
1.1 Definition av waferdicing
Waferdicing (även känt som scribing) är ett viktigt steg i halvledartillverkning, som syftar till att dela upp bearbetade wafers i flera individuella brickor. Dessa brickor innehåller vanligtvis komplett kretsfunktionalitet och är de kärnkomponenter som slutligen används i produktionen av elektroniska enheter. I takt med att chipdesigner blir mer komplexa och dimensionerna fortsätter att krympa, blir precisions- och effektivitetskraven för waferdicing-teknik allt strängare.
I praktiken använder man vid wafer-dicing vanligtvis högprecisionsverktyg som diamantklingor för att säkerställa att varje form förblir intakt och fullt funktionell. Viktiga steg inkluderar förberedelse före skärning, exakt kontroll under skärprocessen och kvalitetsinspektion efter skärning.
Före skärning måste wafern märkas och placeras för att säkerställa exakta skärbanor. Under skärningen måste parametrar som verktygstryck och hastighet kontrolleras noggrant för att förhindra skador på wafern. Efter skärningen utförs omfattande kvalitetsinspektioner för att säkerställa att varje chip uppfyller prestandastandarder.
De grundläggande principerna för wafer-dicing-teknik omfattar inte bara valet av skärutrustning och inställningen av processparametrar utan även inverkan av materialens mekaniska egenskaper på skärkvaliteten. Till exempel är dielektriska kiselskivor med lågt k-innehåll, på grund av sina sämre mekaniska egenskaper, mycket känsliga för spänningskoncentration under skärning, vilket leder till fel som flisning och sprickbildning. Den låga hårdheten och sprödheten hos material med lågt k-innehåll gör dem mer benägna att skadas av mekanisk kraft eller termisk stress, särskilt under skärning. Kontakten mellan verktyget och waferytan, i kombination med höga temperaturer, kan ytterligare förvärra spänningskoncentrationen.
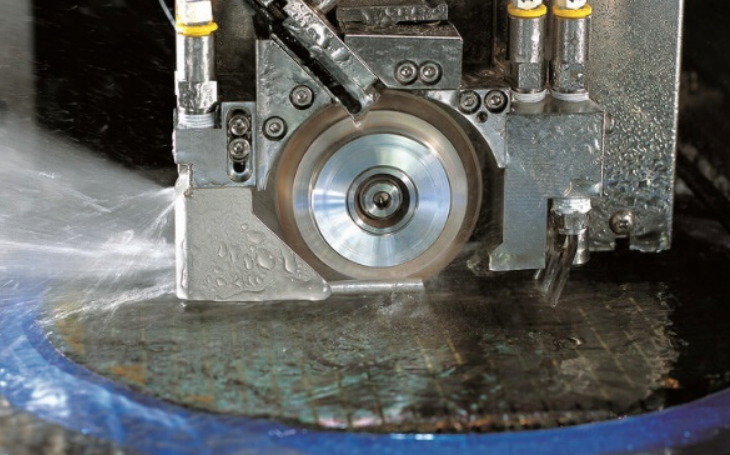
Med framsteg inom materialvetenskap har wafer-diceringstekniken expanderat bortom traditionella kiselbaserade halvledare till att inkludera nya material som galliumnitrid (GaN). Dessa nya material, på grund av sin hårdhet och strukturella egenskaper, innebär nya utmaningar för diceringsprocesser, vilket kräver ytterligare förbättringar av skärverktyg och tekniker.
Som en kritisk process inom halvledarindustrin fortsätter waferdicing att optimeras som svar på utvecklande krav och tekniska framsteg, vilket lägger grunden för framtida mikroelektronik och integrerade kretstekniker.
Förbättringar inom wafer-diceringstekniken går utöver utveckling av hjälpmaterial och verktyg. De omfattar även processoptimering, förbättringar av utrustningens prestanda och exakt kontroll av diceringsparametrar. Dessa framsteg syftar till att säkerställa hög precision, effektivitet och stabilitet i wafer-diceringsprocessen, vilket möter halvledarindustrins behov av mindre dimensioner, högre integration och mer komplexa chipstrukturer.
förbättringsområde | Specifika åtgärder | Effekter |
Processoptimering | - Förbättra de inledande förberedelserna, såsom mer exakt waferpositionering och banplanering. | - Minska skärfel och förbättra stabiliteten. |
- Minimera skärfel och förbättra stabiliteten. | - Använd realtidsövervaknings- och feedbackmekanismer för att justera verktygstryck, hastighet och temperatur. | |
- Lägre andel waferbrott och förbättrad chipkvalitet. | ||
Förbättring av utrustningens prestanda | - Använda högprecisionsmekaniska system och avancerad automationsstyrteknik. | - Förbättra skärnoggrannheten och minska materialspill. |
- Introducera laserskärningsteknik lämplig för wafers med hög hårdhet. | - Förbättra produktionseffektiviteten och minska manuella fel. | |
- Öka automatiseringen av utrustningen för automatisk övervakning och justeringar. | ||
Exakt parameterkontroll | - Finjustera parametrar som skärdjup, hastighet, verktygstyp och kylmetoder. | - Säkerställ brickans integritet och elektriska prestanda. |
- Anpassa parametrar baserat på wafermaterial, tjocklek och struktur. | - Öka avkastningen, minska materialspill och sänka produktionskostnaderna. | |
Strategisk betydelse | - Kontinuerligt utforska nya tekniska vägar, optimera processer och förbättra utrustningens kapacitet för att möta marknadens krav. | - Förbättra avkastning och prestanda vid chiptillverkning, genom att stödja utvecklingen av nya material och avancerade chipdesigner. |
1.2 Vikten av waferdicing
Waferdicing spelar en avgörande roll i halvledartillverkningsprocessen och påverkar direkt efterföljande steg samt slutproduktens kvalitet och prestanda. Dess betydelse kan specificeras enligt följande:
För det första är noggrannheten och konsekvensen i dicingen avgörande för att säkerställa chipets utbyte och tillförlitlighet. Under tillverkningen genomgår wafers flera bearbetningssteg för att bilda ett flertal invecklade kretsstrukturer, vilka måste delas upp exakt i individuella chips (dies). Om det uppstår betydande fel i justering eller skärning under dicingprocessen kan kretsarna skadas, vilket påverkar chipets funktionalitet och tillförlitlighet. Därför säkerställer högprecisionsdicingteknik inte bara varje chip integritet utan förhindrar också skador på interna kretsar, vilket förbättrar den totala utbytesgraden.
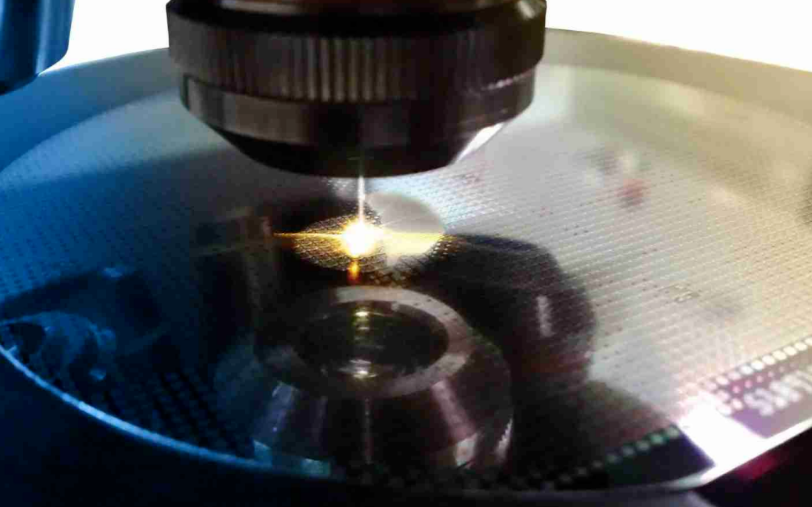
För det andra har wafer-dicering en betydande inverkan på produktionseffektivitet och kostnadskontroll. Som ett avgörande steg i tillverkningsprocessen påverkar dess effektivitet direkt framstegen i efterföljande steg. Genom att optimera diceringsprocessen, öka automatiseringsnivåerna och förbättra skärhastigheterna kan den totala produktionseffektiviteten förbättras avsevärt.
Å andra sidan är materialspill under skärning en avgörande faktor för kostnadshantering. Att använda avancerad skärningsteknik minskar inte bara onödiga materialförluster under skärprocessen utan ökar också waferutnyttjandet, vilket sänker produktionskostnaderna.
Med framsteg inom halvledarteknik fortsätter waferdiametrarna att öka, och kretstätheterna ökar i motsvarande grad, vilket ställer högre krav på dicing-tekniken. Större wafers kräver mer exakt kontroll av skärbanor, särskilt i områden med hög kretstäthet, där även mindre avvikelser kan göra flera chip defekta. Dessutom involverar större wafers fler skärlinjer och mer komplexa processteg, vilket kräver ytterligare förbättringar av dicing-teknikernas precision, konsekvens och effektivitet för att möta dessa utmaningar.
1.3 Wafer-tärningsprocess
Wafer-tärningsprocessen omfattar alla steg från förberedelsefasen till den slutliga kvalitetskontrollen, där varje steg är avgörande för att säkerställa kvaliteten och prestandan hos de tärnade chipsen. Nedan följer en detaljerad förklaring av varje fas.
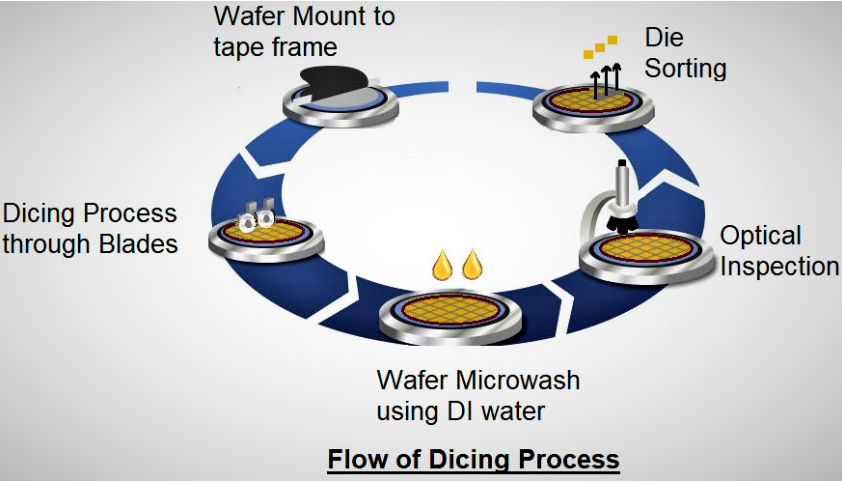
Fas | Detaljerad beskrivning |
Förberedelsefas | -Rengöring av skivorAnvänd rent vatten och specialrengöringsmedel, i kombination med ultraljuds- eller mekanisk skrubbning, för att avlägsna föroreningar, partiklar och föroreningar, vilket säkerställer en ren yta. -Exakt positioneringAnvänd högprecisionsutrustning för att säkerställa att wafern är korrekt uppdelad längs de utformade skärbanorna. -WaferfixeringFäst wafern på en tejpram för att bibehålla stabilitet under skärning, vilket förhindrar skador från vibrationer eller rörelse. |
Skärfas | -KnivskärningAnvänd diamantbelagda blad med hög hastighet för fysisk skärning, lämpliga för kiselbaserade material och kostnadseffektiva. -LaserutskärningAnvänd högenergilaserstrålar för beröringsfri skärning, idealiskt för spröda eller hårda material som galliumnitrid, vilket ger högre precision och mindre materialförlust. -Nya teknologierIntroducera laser- och plasmaskärningsteknik för att ytterligare förbättra effektivitet och precision samtidigt som värmepåverkade zoner minimeras. |
Rengöringsfas | - Använd avjoniserat vatten (DI-vatten) och specialiserade rengöringsmedel, i kombination med ultraljuds- eller sprayrengöring, för att avlägsna skräp och damm som genereras under skärning, vilket förhindrar att rester påverkar efterföljande processer eller spånans elektriska prestanda. - Högrent destillerat vatten undviker att nya föroreningar införs, vilket säkerställer en ren wafermiljö. |
Inspektionsfas | -Optisk inspektionAnvänd optiska detekteringssystem i kombination med AI-algoritmer för att snabbt identifiera defekter, säkerställa att det inte finns några sprickor eller flisor i de tärnade flisorna, förbättra inspektionseffektiviteten och minska mänskliga fel. -DimensionsmätningKontrollera att chipets dimensioner uppfyller designspecifikationerna. -Elektrisk prestandatestningSäkerställ att kritiska chips elektriska prestanda uppfyller standarder, vilket garanterar tillförlitlighet i efterföljande tillämpningar. |
Sorteringsfas | - Använd robotarmar eller sugkoppar för att separera kvalificerade chips från bandramen och sortera dem automatiskt baserat på prestanda, vilket säkerställer produktionseffektivitet och flexibilitet samtidigt som precisionen förbättras. |
Waferskärningsprocessen innefattar rengöring, positionering, skärning, rengöring, inspektion och sortering av wafers, där varje steg är avgörande. Med framsteg inom automatisering, laserskärning och AI-inspektionsteknik kan moderna waferskärningssystem uppnå högre precision, hastighet och lägre materialförlust. I framtiden kommer nya skärtekniker som laser och plasma gradvis att ersätta traditionell bladskärning för att möta behoven hos alltmer komplexa chipdesigner, vilket ytterligare driver utvecklingen av halvledartillverkningsprocesser.
Waferskärningsteknik och dess principer
Bilden illustrerar tre vanliga waferskärningstekniker:Knivskärning,LaserutskärningochPlasma-tärningNedan följer en detaljerad analys och kompletterande förklaring av dessa tre tekniker:
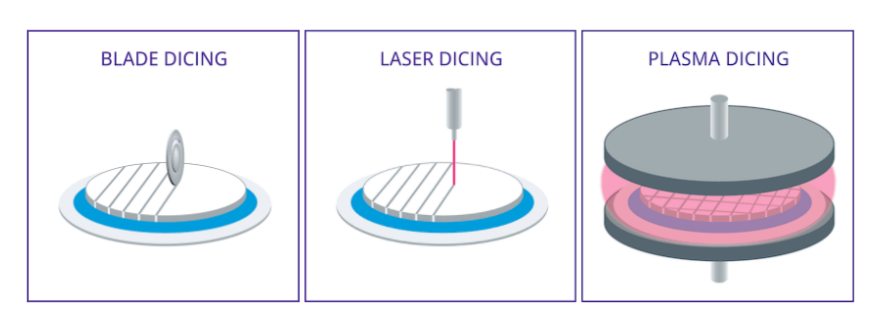
Inom halvledartillverkning är skivskärning ett avgörande steg som kräver att man väljer lämplig skärmetod baserat på skivans tjocklek. Det första steget är att bestämma skivans tjocklek. Om skivans tjocklek överstiger 100 mikron kan bladskärning väljas som skärmetod. Om bladskärning inte är lämplig kan frakturskärningsmetoden användas, vilket inkluderar både ritsskärning och bladskärning.
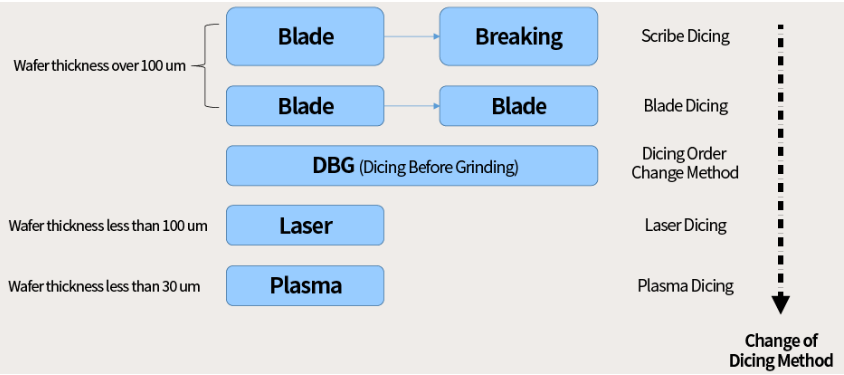
När skivans tjocklek är mellan 30 och 100 mikron rekommenderas DBG-metoden (Dice Before Grinding). I detta fall kan man välja ritsning, bladskärning eller justering av skärsekvensen efter behov för att uppnå bästa resultat.
För ultratunna wafers med en tjocklek på mindre än 30 mikron blir laserskärning den föredragna metoden på grund av dess förmåga att skära tunna wafers exakt utan att orsaka alltför stora skador. Om laserskärning inte kan uppfylla specifika krav kan plasmaskärning användas som ett alternativ. Detta flödesschema ger en tydlig beslutsväg för att säkerställa att den mest lämpliga waferskärningstekniken väljs under olika tjockleksförhållanden.
2.1 Mekanisk skärteknik
Mekanisk skärteknik är den traditionella metoden för wafer-dicering. Kärnprincipen är att använda en höghastighetsroterande diamantslipskiva som skärverktyg för att skära skivan. Nyckelutrustningen inkluderar en luftlagrad spindel, som driver diamantslipskivan med höga hastigheter för att utföra exakt skärning eller spårfräsning längs en fördefinierad skärbana. Denna teknik används ofta inom industrin på grund av dess låga kostnad, höga effektivitet och breda tillämpbarhet.
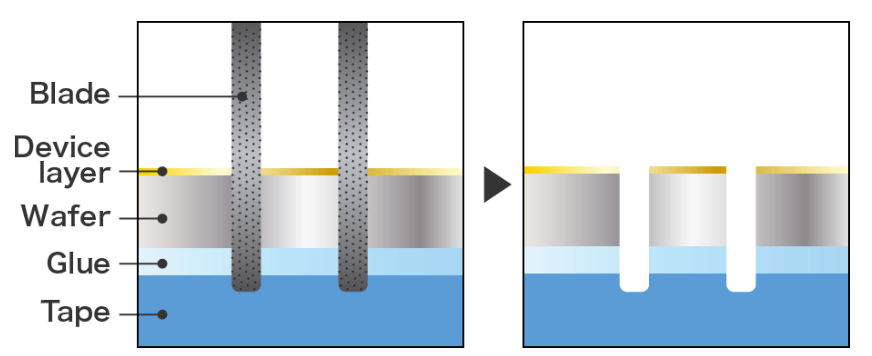
Fördelar
Den höga hårdheten och slitstyrkan hos diamantslipskivor gör att mekanisk skärteknik kan anpassas till skärbehoven hos olika wafermaterial, oavsett om det är traditionella kiselbaserade material eller nyare sammansatta halvledare. Dess funktion är enkel, med relativt låga tekniska krav, vilket ytterligare främjar dess popularitet inom massproduktion. Dessutom, jämfört med andra skärmetoder som laserskärning, har mekanisk skärning mer kontrollerbara kostnader, vilket gör den lämplig för produktionsbehov i hög volym.
Begränsningar
Trots sina många fördelar har mekanisk skärteknik också begränsningar. För det första, på grund av den fysiska kontakten mellan verktyget och wafern, är skärprecisionen relativt begränsad, vilket ofta leder till dimensionsavvikelser som kan påverka noggrannheten i efterföljande chippaketering och testning. För det andra kan defekter som flisning och sprickor lätt uppstå under den mekaniska skärprocessen, vilket inte bara påverkar utbytet utan också kan ha en negativ inverkan på chipens tillförlitlighet och livslängd. De mekaniska stressinducerade skadorna är särskilt skadliga för högdensitetschiptillverkning, särskilt vid skärning av spröda material, där dessa problem är mer framträdande.
Teknologiska förbättringar
För att övervinna dessa begränsningar optimerar forskare kontinuerligt den mekaniska skärprocessen. Viktiga förbättringar inkluderar förbättrad design och materialval av slipskivor för att förbättra skärprecision och hållbarhet. Dessutom har optimering av den strukturella designen och styrsystemen för skärutrustning ytterligare förbättrat stabiliteten och automatiseringen av skärprocessen. Dessa framsteg minskar fel orsakade av mänskliga operationer och förbättrar skärningarnas konsistens. Införandet av avancerad inspektions- och kvalitetskontrollteknik för realtidsövervakning av avvikelser under skärprocessen har också avsevärt förbättrat skärtillförlitligheten och utbytet.
Framtida utveckling och nya teknologier
Även om mekanisk skärteknik fortfarande har en betydande position inom waferskärning, utvecklas nya skärtekniker snabbt i takt med att halvledarprocesser utvecklas. Till exempel ger tillämpningen av termisk laserskärteknik nya lösningar på precisions- och defektproblem vid mekanisk skärning. Denna kontaktfria skärmetod minskar den fysiska belastningen på wafern, vilket avsevärt minskar förekomsten av flisning och sprickbildning, särskilt vid skärning av mer spröda material. I framtiden kommer integrationen av mekanisk skärteknik med nya skärtekniker att ge halvledartillverkning fler alternativ och flexibilitet, vilket ytterligare förbättrar tillverkningseffektiviteten och chipkvaliteten.
Sammanfattningsvis, även om mekanisk skärteknik har vissa nackdelar, gör kontinuerliga tekniska förbättringar och dess integration med nya skärtekniker att den fortfarande kan spela en viktig roll inom halvledartillverkning och bibehålla sin konkurrenskraft i framtida processer.
2.2 Laserskärningsteknik
Laserskärningstekniken, som en ny metod för waferskärning, har gradvis fått stor uppmärksamhet inom halvledarindustrin på grund av dess höga precision, brist på mekanisk kontaktskada och snabba skärkapacitet. Denna teknik använder laserstrålens höga energitäthet och fokuseringsförmåga för att skapa en liten värmepåverkad zon på wafermaterialets yta. När laserstrålen appliceras på wafern orsakar den genererade termiska spänningen att materialet spricker på den angivna platsen, vilket uppnår exakt skärning.
Fördelar med laserskärningsteknik
• Hög precisionLaserstrålens exakta positioneringsförmåga möjliggör skärprecision på mikron- eller till och med nanometernivå, vilket uppfyller kraven för modern högprecisionstillverkning av integrerade kretsar med hög densitet.
• Ingen mekanisk kontaktLaserskärning undviker fysisk kontakt med wafern, vilket förhindrar vanliga problem vid mekanisk skärning, såsom flisning och sprickbildning, vilket avsevärt förbättrar chipens utbyte och tillförlitlighet.
• Snabb skärhastighetLaserskärningens höga hastighet bidrar till ökad produktionseffektivitet, vilket gör den särskilt lämplig för storskaliga produktionsscenarier med hög hastighet.
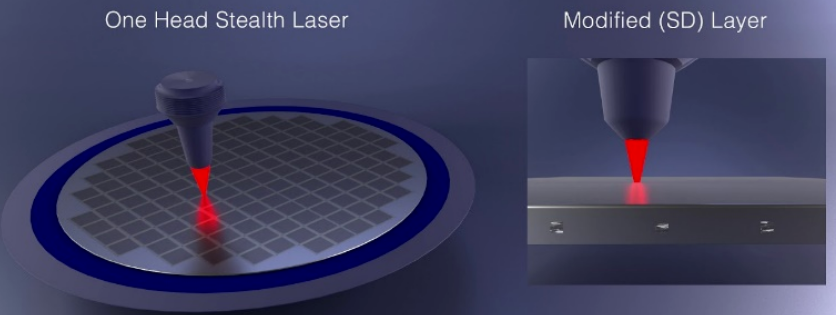
Utmaningar som ställs inför
• Hög utrustningskostnadDen initiala investeringen för laserskärningsutrustning är hög, vilket innebär ekonomisk press, särskilt för små och medelstora produktionsföretag.
• Komplex processkontrollLaserskärning kräver exakt kontroll av flera parametrar, inklusive energitäthet, fokusposition och skärhastighet, vilket gör processen komplex.
• Problem med värmepåverkade zonerÄven om laserskärningens beröringsfria natur minskar mekaniska skador, kan den termiska stressen som orsakas av den värmepåverkade zonen (HAZ) negativt påverka wafermaterialets egenskaper. Ytterligare optimering av processen behövs för att minimera denna effekt.
Teknologiska förbättringsriktningar
För att hantera dessa utmaningar fokuserar forskare på att sänka utrustningskostnaderna, förbättra skäreffektiviteten och optimera processflödet.
• Effektiva lasrar och optiska systemGenom att utveckla effektivare lasrar och avancerade optiska system är det möjligt att sänka utrustningskostnaderna samtidigt som skärprecisionen och hastigheten förbättras.
• Optimering av processparametrarDjupgående forskning om samspelet mellan lasrar och wafermaterial bedrivs för att förbättra processer som minskar den värmepåverkade zonen och därigenom förbättrar skärkvaliteten.
• Intelligenta styrsystemUtvecklingen av intelligent styrteknik syftar till att automatisera och optimera laserskärningsprocessen, vilket förbättrar dess stabilitet och konsekvens.
Laserskärningsteknik är särskilt effektiv i ultratunna wafers och högprecisionsskärningsscenarier. I takt med att waferstorlekarna ökar och kretstätheterna stiger, kämpar traditionella mekaniska skärmetoder för att möta de högprecisions- och högeffektivitetskrav som modern halvledartillverkning kräver. På grund av sina unika fördelar blir laserskärning den föredragna lösningen inom dessa områden.
Även om laserskärningstekniken fortfarande står inför utmaningar som höga utrustningskostnader och processkomplexitet, gör dess unika fördelar med hög precision och kontaktfria skador den till en viktig utvecklingsriktning inom halvledartillverkning. I takt med att lasertekniken och intelligenta styrsystem fortsätter att utvecklas förväntas laserskärning ytterligare förbättra effektiviteten och kvaliteten vid skivskärning, vilket driver den kontinuerliga utvecklingen av halvledarindustrin.
2.3 Plasmaskärningsteknik
Plasmaskärningsteknik, som en framväxande wafer-dicing-metod, har fått stor uppmärksamhet de senaste åren. Denna teknik använder högenergiplasmastrålar för att exakt skära wafers genom att kontrollera plasmastrålens energi, hastighet och skärbana, vilket uppnår optimala skärresultat.
Arbetsprincip och fördelar
Plasmaskärningsprocessen använder en högtemperatur- och högenergiplasmastråle som genereras av utrustningen. Denna stråle kan värma upp wafermaterialet till dess smält- eller förångningspunkt på mycket kort tid, vilket möjliggör snabb skärning. Jämfört med traditionell mekanisk skärning eller laserskärning är plasmaskärning snabbare och producerar en mindre värmepåverkad zon, vilket effektivt minskar förekomsten av sprickor och skador under skärning.
I praktiska tillämpningar är plasmaskärningstekniken särskilt skicklig på att hantera wafers med komplexa former. Dess högenergiska, justerbara plasmastråle kan enkelt skära oregelbundet formade wafers med hög precision. Därför, inom mikroelektroniktillverkning, särskilt vid kundanpassad och småskalig produktion av avancerade chips, visar denna teknik stort potential för utbredd användning.
Utmaningar och begränsningar
Trots de många fördelarna med plasmaskärningsteknik står den också inför vissa utmaningar.
• Komplex processPlasmaskärningsprocessen är komplex och kräver högprecisionsutrustning och erfarna operatörer för att säkerställanoggrannhet och stabilitet vid skärning.
• Miljökontroll och säkerhetPlasmastrålens höga temperatur och höga energi kräver stränga miljökontroll- och säkerhetsåtgärder, vilket ökar komplexiteten och kostnaden för implementeringen.
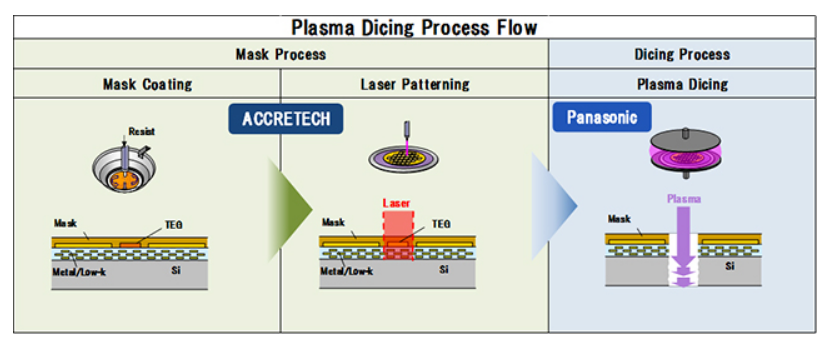
Framtida utvecklingsriktningar
Med tekniska framsteg förväntas utmaningarna i samband med plasmaskärning gradvis övervinnas. Genom att utveckla smartare och mer stabil skärutrustning kan beroendet av manuella operationer minskas, vilket förbättrar produktionseffektiviteten. Samtidigt kommer optimering av processparametrar och skärmiljön att bidra till att minska säkerhetsrisker och driftskostnader.
Inom halvledarindustrin är innovationer inom waferskärning och dicing-teknik avgörande för att driva branschens utveckling. Plasmaskärningstekniken, med sin höga precision, effektivitet och förmåga att hantera komplexa waferformer, har framträtt som en betydande ny aktör inom detta område. Även om vissa utmaningar kvarstår, kommer dessa problem gradvis att åtgärdas med fortsatt teknisk innovation, vilket ger fler möjligheter och möjligheter till halvledartillverkning.
Tillämpningsmöjligheterna för plasmaskärningsteknik är enorma och den förväntas spela en allt viktigare roll inom halvledartillverkning i framtiden. Genom kontinuerlig teknisk innovation och optimering kommer plasmaskärning inte bara att ta itu med befintliga utmaningar utan också bli en kraftfull drivkraft för halvledarindustrins tillväxt.
2.4 Skärkvalitet och påverkande faktorer
Kvaliteten på skivskärning är avgörande för den efterföljande spånförpackningen, testningen och slutproduktens övergripande prestanda och tillförlitlighet. Vanliga problem som uppstår vid skärning inkluderar sprickor, flisning och skäravvikelser. Dessa problem påverkas av flera faktorer som samverkar.
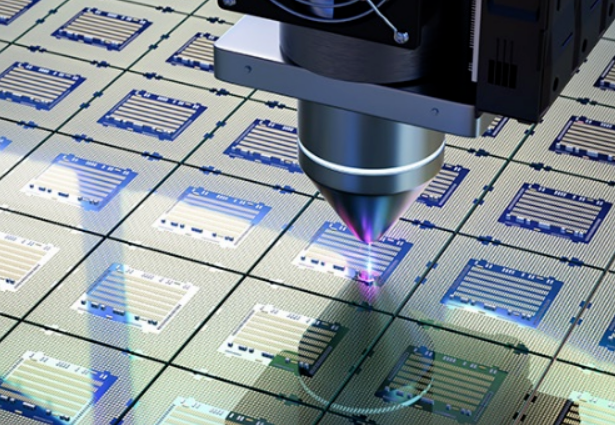
Kategori | Innehåll | Inverkan |
Processparametrar | Skärhastighet, matningshastighet och skärdjup påverkar direkt stabiliteten och precisionen i skärprocessen. Felaktiga inställningar kan leda till spänningskoncentration och överdriven värmepåverkad zon, vilket resulterar i sprickor och flisning. Att justera parametrar på lämpligt sätt baserat på wafermaterial, tjocklek och skärkrav är nyckeln till att uppnå önskade skärresultat. | Rätt processparametrar säkerställer exakt skärning och minskar risken för defekter som sprickor och flisning. |
Utrustnings- och materialfaktorer | -BladkvalitetBladets material, hårdhet och slitstyrka påverkar skärprocessens jämnhet och skärytans planhet. Blad av dålig kvalitet ökar friktion och termisk stress, vilket kan leda till sprickor eller flisning. Att välja rätt bladmaterial är avgörande. -KylvätskeprestandaKylvätskor hjälper till att minska skärtemperaturen, minimera friktion och avlägsna skräp. Ineffektiv kylvätska kan leda till höga temperaturer och skräpansamling, vilket påverkar skärkvaliteten och effektiviteten. Att välja effektiva och miljövänliga kylvätskor är avgörande. | Bladkvaliteten påverkar snittets precision och jämnhet. Ineffektiv kylvätska kan resultera i dålig skärkvalitet och effektivitet, vilket betonar behovet av optimal kylvätskasanvändning. |
Processkontroll och kvalitetsinspektion | -ProcesskontrollRealtidsövervakning och justering av viktiga skärparametrar för att säkerställa stabilitet och konsekvens i skärprocessen. -KvalitetsinspektionKontroller av utseende efter skärning, dimensionsmätningar och elektriska prestandatester hjälper till att identifiera och åtgärda kvalitetsproblem snabbt, vilket förbättrar skärnoggrannheten och konsekvensen. | Korrekt processkontroll och kvalitetsinspektion bidrar till att säkerställa konsekventa, högkvalitativa skärresultat och tidig upptäckt av potentiella problem. |

Förbättra skärkvaliteten
Förbättrad skärkvalitet kräver en omfattande strategi som tar hänsyn till processparametrar, utrustnings- och materialval, processkontroll och inspektion. Genom att kontinuerligt förfina skärtekniker och optimera processmetoder kan precisionen och stabiliteten vid waferskärning förbättras ytterligare, vilket ger ett mer tillförlitligt tekniskt stöd för halvledartillverkningsindustrin.
#03 Hantering och testning efter skärning
3.1 Rengöring och torkning
Rengörings- och torkningsstegen efter waferskärning är avgörande för att säkerställa chipskvaliteten och en smidig fortskridande process. Under detta steg är det viktigt att noggrant avlägsna kiselrester, kylvätskerester och andra föroreningar som genereras under skärningen. Det är lika viktigt att säkerställa att chipsen inte skadas under rengöringsprocessen, och efter torkning, se till att ingen fukt finns kvar på chipytan för att förhindra problem som korrosion eller elektrostatisk urladdning.
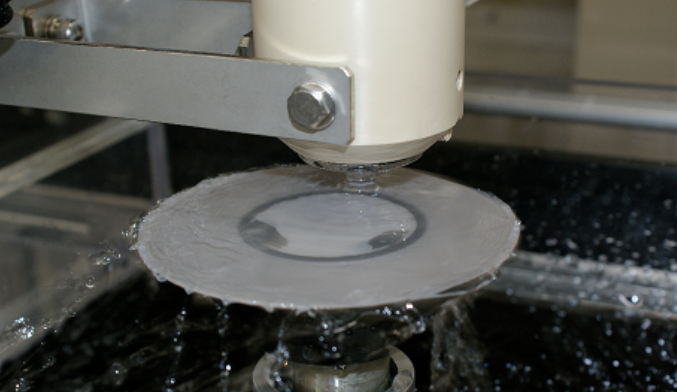
Hantering efter skärning: Rengörings- och torkningsprocess
Processsteg | Innehåll | Inverkan |
Rengöringsprocess | -MetodAnvänd specialrengöringsmedel och rent vatten i kombination med ultraljuds- eller mekaniska borstningstekniker för rengöring. | Säkerställer noggrann borttagning av föroreningar och förhindrar skador på flisorna under rengöring. |
-Val av rengöringsmedelVälj baserat på wafermaterial och föroreningstyp för att säkerställa effektiv rengöring utan att skada chipet. | Rätt val av rengöringsmedel är nyckeln till effektiv rengöring och flisskydd. | |
-ParameterkontrollKontrollera noggrant rengöringstemperatur, tid och koncentration av rengöringslösning för att förhindra kvalitetsproblem orsakade av felaktig rengöring. | Kontroller hjälper till att undvika att skada wafern eller lämna kvar föroreningar, vilket säkerställer en jämn kvalitet. | |
Torkningsprocess | -Traditionella metoderNaturlig lufttorkning och varmluftstorkning, vilka har låg effektivitet och kan leda till uppbyggnad av statisk elektricitet. | Kan resultera i långsammare torktider och potentiella problem med statisk elektricitet. |
-Moderna teknologierAnvänd avancerad teknik som vakuumtorkning och infrarödtorkning för att säkerställa att flisorna torkar snabbt och undviker skadliga effekter. | Snabbare och effektivare torkningsprocess, vilket minskar risken för statisk elektricitet eller fuktrelaterade problem. | |
Utrustningsval och underhåll | -UtrustningsvalHögpresterande rengörings- och torkmaskiner förbättrar bearbetningseffektiviteten och kontrollerar potentiella problem under hanteringen noggrant. | Högkvalitativa maskiner säkerställer bättre bearbetning och minskar risken för fel vid rengöring och torkning. |
-UtrustningsunderhållRegelbunden inspektion och underhåll av utrustningen säkerställer att den förblir i optimalt skick och garanterar flisens kvalitet. | Korrekt underhåll förhindrar utrustningsfel och säkerställer pålitlig och högkvalitativ bearbetning. |
Rengöring och torkning efter skärning
Rengörings- och torkningsstegen efter waferskärning är komplexa och känsliga processer som kräver noggrant övervägande av flera faktorer för att säkerställa det slutliga bearbetningsresultatet. Genom att använda vetenskapliga metoder och rigorösa procedurer är det möjligt att säkerställa att varje chip går in i de efterföljande förpacknings- och teststegen i optimalt skick.
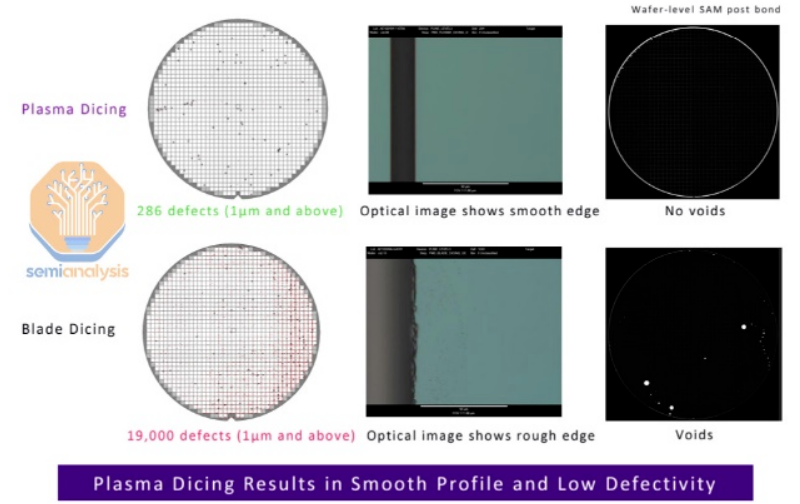
Inspektion och testning efter skärning
Steg | Innehåll | Inverkan |
Inspektionssteg | 1.Visuell inspektionAnvänd visuell eller automatiserad inspektionsutrustning för att kontrollera synliga defekter som sprickor, flisor eller kontaminering på spånytan. Identifiera snabbt fysiskt skadade spånor för att undvika spill. | Hjälper till att identifiera och eliminera defekta spånor tidigt i processen, vilket minskar materialförlust. |
2.StorleksmätningAnvänd precisionsmätinstrument för att noggrant mäta spåndimensioner, säkerställa att den skurna storleken uppfyller designspecifikationerna och förhindra prestandaproblem eller förpackningssvårigheter. | Säkerställer att chipsen håller sig inom de erforderliga storleksgränserna, vilket förhindrar prestandaförsämring eller monteringsproblem. | |
3.Elektrisk prestandatestningUtvärdera viktiga elektriska parametrar som resistans, kapacitans och induktans för att identifiera chip som inte uppfyller kraven och säkerställa att endast prestandakvalificerade chip går vidare till nästa steg. | Säkerställer att endast funktionella och prestandatestade chips går vidare i processen, vilket minskar risken för fel i senare skeden. | |
Teststeg | 1.Funktionell testningKontrollera att chipets grundläggande funktioner fungerar som avsett, identifiera och eliminera chips med funktionella avvikelser. | Säkerställer att chips uppfyller grundläggande driftskrav innan de går vidare till senare steg. |
2.TillförlitlighetstestningUtvärdera chipets prestanda och stabilitet under långvarig användning eller tuffa miljöer, vanligtvis med högtemperaturåldring, lågtemperaturtestning och fuktighetstestning för att simulera verkliga extrema förhållanden. | Säkerställer att chips kan fungera tillförlitligt under en rad olika miljöförhållanden, vilket förbättrar produktens livslängd och stabilitet. | |
3.KompatibilitetstestningKontrollera att chipet fungerar korrekt med andra komponenter eller system och se till att det inte finns några fel eller prestandaförsämring på grund av inkompatibilitet. | Säkerställer smidig drift i verkliga applikationer genom att förhindra kompatibilitetsproblem. |
3.3 Förpackning och förvaring
Efter waferskärning är chipen en avgörande del av halvledartillverkningsprocessen, och deras förpacknings- och lagringsfaser är lika viktiga. Korrekt förpacknings- och lagringsåtgärder är avgörande, inte bara för att säkerställa chipens säkerhet och stabilitet under transport och lagring, utan också för att ge starkt stöd för efterföljande produktions-, test- och förpackningsfaser.
Sammanfattning av inspektions- och testningsfaser:
Inspektions- och teststegen för chip efter waferskärning omfattar en rad aspekter, inklusive visuell inspektion, storleksmätning, elektrisk prestandatestning, funktionstestning, tillförlitlighetstestning och kompatibilitetstestning. Dessa steg är sammankopplade och kompletterar varandra och bildar en solid barriär för att säkerställa produktkvalitet och tillförlitlighet. Genom strikta inspektions- och testprocedurer kan potentiella problem identifieras och lösas snabbt, vilket säkerställer att slutprodukten uppfyller kundernas krav och förväntningar.
Aspekt | Innehåll |
Förpackningsåtgärder | 1.AntistatiskFörpackningsmaterial bör ha utmärkta antistatiska egenskaper för att förhindra att statisk elektricitet skadar enheterna eller påverkar deras prestanda. |
2.FukttätFörpackningsmaterial bör ha god fuktbeständighet för att förhindra korrosion och försämring av elektrisk prestanda orsakad av fuktighet. | |
3.StötsäkerFörpackningsmaterialen bör ge effektiv stötdämpning för att skydda chipsen från vibrationer och slag under transport. | |
Lagringsmiljö | 1.FuktighetskontrollKontrollera luftfuktigheten noggrant inom ett lämpligt intervall för att förhindra fuktabsorption och korrosion orsakad av för hög luftfuktighet eller statiska problem orsakade av låg luftfuktighet. |
2.RenlighetUpprätthåll en ren förvaringsmiljö för att undvika kontaminering av flisor med damm och föroreningar. | |
3.TemperaturkontrollStäll in ett rimligt temperaturintervall och bibehåll temperaturstabilitet för att förhindra accelererat åldrande på grund av överdriven värme eller kondensproblem orsakade av låga temperaturer. | |
Regelbunden inspektion | Inspektera och utvärdera regelbundet lagrade chips med hjälp av visuella inspektioner, storleksmätningar och elektriska prestandatester för att identifiera och åtgärda potentiella problem i tid. Planera användningen av chips baserat på lagringstid och förhållanden för att säkerställa att de används i optimalt skick. |
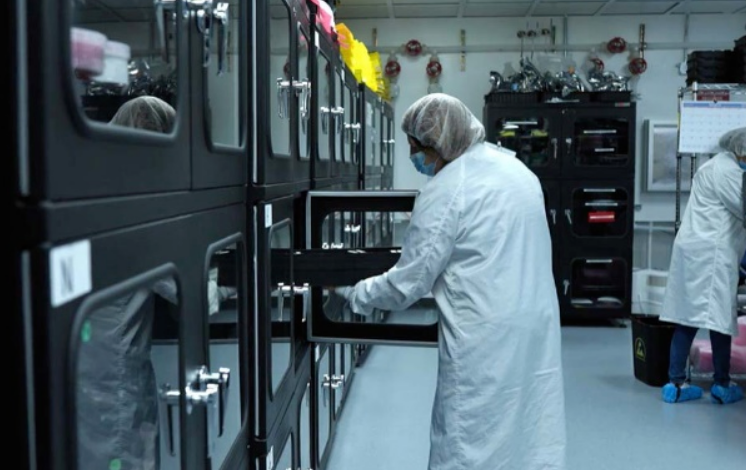
Problemet med mikrosprickor och skador under wafer-skärningsprocessen är en betydande utmaning inom halvledartillverkning. Skärspänningen är den främsta orsaken till detta fenomen, eftersom den skapar små sprickor och skador på waferns yta, vilket leder till ökade tillverkningskostnader och en minskad produktkvalitet.
För att hantera denna utmaning är det avgörande att minimera skärspänningen och implementera optimerade skärtekniker, verktyg och förhållanden. Noggrann uppmärksamhet på faktorer som bladmaterial, skärhastighet, tryck och kylmetoder kan bidra till att minska bildandet av mikrosprickor och förbättra processens totala utbyte. Dessutom undersöker pågående forskning om mer avancerade skärtekniker, såsom laserskärning, sätt att ytterligare mildra dessa problem.
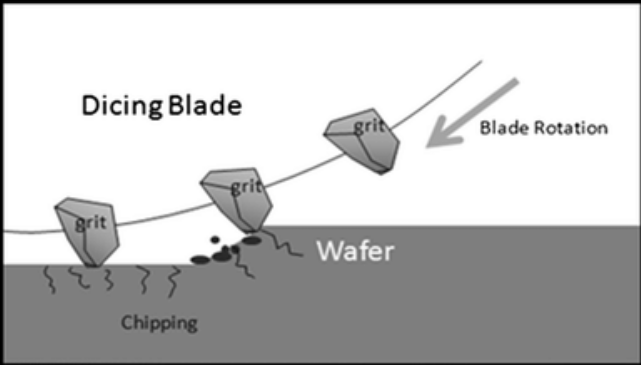
Eftersom wafers är ett ömtåligt material är de benägna att förändras internt i strukturen när de utsätts för mekanisk, termisk eller kemisk stress, vilket leder till bildandet av mikrosprickor. Även om dessa sprickor kanske inte är omedelbart märkbara kan de expandera och orsaka allvarligare skador allt eftersom tillverkningsprocessen fortskrider. Detta problem blir särskilt problematiskt under efterföljande förpacknings- och testningssteg, där temperaturfluktuationer och ytterligare mekaniska påfrestningar kan få dessa mikrosprickor att utvecklas till synliga sprickor, vilket potentiellt kan leda till chipfel.
För att minska denna risk är det viktigt att noggrant kontrollera skärprocessen genom att optimera parametrar som skärhastighet, tryck och temperatur. Att använda mindre aggressiva skärmetoder, såsom laserskärning, kan minska den mekaniska belastningen på wafern och minimera bildandet av mikrosprickor. Dessutom kan implementering av avancerade inspektionsmetoder som infraröd skanning eller röntgenavbildning under waferskärningsprocessen hjälpa till att upptäcka dessa sprickor i tidigt skede innan de orsakar ytterligare skador.
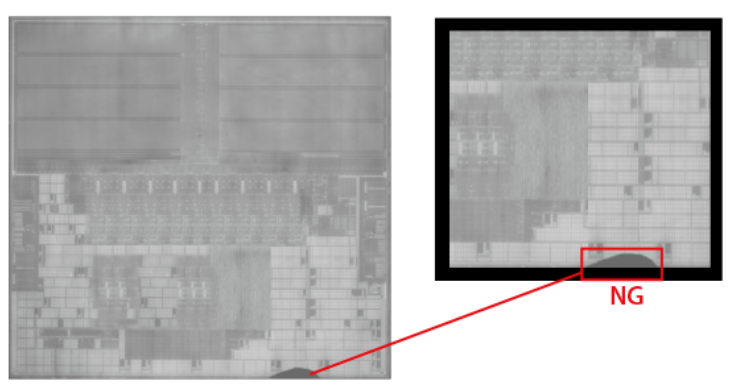
Skador på waferns yta är ett betydande problem i skärprocessen, eftersom det kan ha en direkt inverkan på chipets prestanda och tillförlitlighet. Sådana skador kan orsakas av felaktig användning av skärverktyg, felaktiga skärparametrar eller materialfel som är inneboende i själva wafern. Oavsett orsak kan dessa skador leda till förändringar i kretsens elektriska resistans eller kapacitans, vilket påverkar den totala prestandan.
För att ta itu med dessa problem undersöks två viktiga strategier:
1. Optimering av skärverktyg och parametrarGenom att använda vassare blad, justera skärhastigheten och modifiera skärdjupet kan spänningskoncentrationen under skärprocessen minimeras, vilket minskar risken för skador.
2. Utforska nya skärteknikerAvancerade tekniker som laserskärning och plasmaskärning erbjuder förbättrad precision samtidigt som de potentiellt minskar skadorna på wafern. Dessa tekniker studeras för att hitta sätt att uppnå hög skärnoggrannhet samtidigt som termisk och mekanisk belastning på wafern minimeras.
Termiskt påverkansområde och dess effekter på prestanda
Vid termiska skärprocesser som laser- och plasmaskärning skapar höga temperaturer oundvikligen en termisk stötzon på waferns yta. Detta område, där temperaturgradienten är betydande, kan förändra materialets egenskaper och påverka chipets slutliga prestanda.
Påverkan av den termiskt påverkade zonen (TAZ):
KristallstrukturförändringarVid höga temperaturer kan atomer i wafermaterialet omorganiseras, vilket orsakar förvrängningar i kristallstrukturen. Denna förvrängning försvagar materialet, minskar dess mekaniska hållfasthet och stabilitet, vilket ökar risken för chipfel under användning.
Förändringar i elektriska egenskaperHöga temperaturer kan förändra bärvågskoncentrationen och rörligheten i halvledarmaterial, vilket påverkar chipets elektriska ledningsförmåga och strömöverföringseffektivitet. Dessa förändringar kan leda till en försämrad prestanda, vilket potentiellt gör det olämpligt för sitt avsedda ändamål.
För att mildra dessa effekter är det viktiga strategier att kontrollera temperaturen under skärning, optimera skärparametrarna och utforska metoder som kylstrålar eller efterbehandlingar för att minska omfattningen av termisk påverkan och bibehålla materialets integritet.
Sammantaget är både mikrosprickor och termiska stötzoner avgörande utmaningar inom waferdicing-tekniken. Fortsatt forskning, tillsammans med tekniska framsteg och kvalitetskontrollåtgärder, kommer att vara nödvändig för att förbättra kvaliteten på halvledarprodukter och öka deras konkurrenskraft på marknaden.
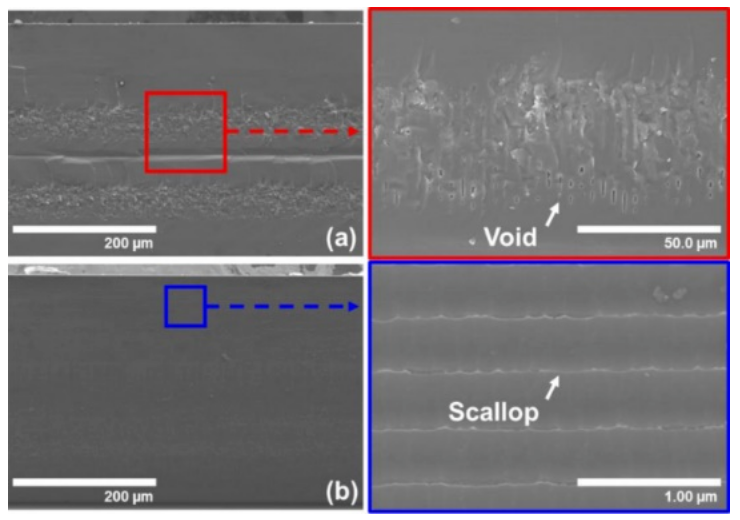
Åtgärder för att kontrollera den termiska påverkanszonen:
Optimera skärprocessparametrarAtt minska skärhastigheten och effekten kan effektivt minimera storleken på den termiska stötzonen (TAZ). Detta hjälper till att kontrollera mängden värme som genereras under skärprocessen, vilket direkt påverkar waferns materialegenskaper.
Avancerade kylteknikerTillämpningen av tekniker som kylning med flytande kväve och mikrofluidisk kylning kan avsevärt begränsa den termiska stötzonens räckvidd. Dessa kylmetoder hjälper till att avleda värme mer effektivt, vilket bevarar waferns materialegenskaper och minimerar termiska skador.
MaterialvalForskare utforskar nya material, såsom kolnanorör och grafen, som har utmärkt värmeledningsförmåga och mekanisk hållfasthet. Dessa material kan minska den termiska stötzonen samtidigt som de förbättrar chipens totala prestanda.
Sammanfattningsvis, även om den termiska stötzonen är en oundviklig konsekvens av termiska skärtekniker, kan den effektivt kontrolleras genom optimerade bearbetningstekniker och materialval. Framtida forskning kommer sannolikt att fokusera på finjustering och automatisering av termiska skärprocesser för att uppnå effektivare och mer exakt waferdikning.

Balansstrategi:
Att uppnå optimal balans mellan waferutbyte och produktionseffektivitet är en ständig utmaning inom waferdikningstekniken. Tillverkare måste beakta flera faktorer, såsom marknadsefterfrågan, produktionskostnader och produktkvalitet, för att utveckla en rationell produktionsstrategi och processparametrar. Samtidigt är det avgörande att införa avancerad skärutrustning, förbättra operatörernas färdigheter och förbättra kvalitetskontrollen av råmaterial för att bibehålla eller till och med förbättra utbytet samtidigt som produktionseffektiviteten ökar.
Framtida utmaningar och möjligheter:
Med utvecklingen av halvledartekniken står waferskärning inför nya utmaningar och möjligheter. I takt med att chipstorlekarna krymper och integrationen ökar, ökar kraven på skärprecision och kvalitet avsevärt. Samtidigt ger nya teknologier nya idéer för utveckling av waferskärningstekniker. Tillverkare måste vara lyhörda för marknadsdynamiken och tekniska trender, och kontinuerligt justera och optimera produktionsstrategier och processparametrar för att möta marknadsförändringar och tekniska krav.
Sammanfattningsvis kan tillverkare, genom att integrera överväganden om marknadsefterfrågan, produktionskostnader och produktkvalitet, och genom att införa avancerad utrustning och teknik, förbättra operatörernas färdigheter och stärka råvarukontrollen, uppnå den bästa balansen mellan waferutbyte och produktionseffektivitet under waferdikning, vilket leder till effektiv och högkvalitativ produktion av halvledarprodukter.
Framtidsutsikter:
Med snabba tekniska framsteg utvecklas halvledartekniken i en aldrig tidigare skådad takt. Som ett kritiskt steg inom halvledartillverkning är waferskärningstekniken redo för spännande nya utvecklingar. Framöver förväntas waferskärningstekniken uppnå betydande förbättringar av precision, effektivitet och kostnad, vilket ger ny vitalitet till den fortsatta tillväxten inom halvledarindustrin.
Ökad precision:
I strävan efter högre precision kommer waferskärningstekniken ständigt att tänja på gränserna för befintliga processer. Genom att djupgående studera de fysikaliska och kemiska mekanismerna i skärprocessen och exakt kontrollera skärparametrar kommer finare skärresultat att uppnås för att möta alltmer komplexa kretsdesignkrav. Dessutom kommer utforskningen av nya material och skärmetoder avsevärt att förbättra utbyte och kvalitet.
Ökad effektivitet:
Ny utrustning för skivskärning kommer att fokusera på smart och automatiserad design. Införandet av avancerade styrsystem och algoritmer kommer att göra det möjligt för utrustningen att automatiskt justera skärparametrar för att anpassa sig till olika material- och designkrav, vilket avsevärt förbättrar produktionseffektiviteten. Innovationer som teknik för skärning av flera skivor och system för snabba bladbyten kommer att spela en avgörande roll för att öka effektiviteten.
Minska kostnader:
Att minska kostnader är en viktig inriktning för utvecklingen av waferskärningsteknik. I takt med att nya material och skärmetoder utvecklas förväntas utrustningskostnader och underhållskostnader kunna kontrolleras effektivt. Dessutom kommer optimering av produktionsprocesser och minskade kassationsnivåer ytterligare att minska avfallet under tillverkningen, vilket leder till en minskning av de totala produktionskostnaderna.
Smart tillverkning och IoT:
Integreringen av smart tillverkning och sakernas internet (IoT)-teknik kommer att medföra omvälvande förändringar inom waferskärningstekniken. Genom sammankoppling och datadelning mellan enheter kan varje steg i produktionsprocessen övervakas och optimeras i realtid. Detta förbättrar inte bara produktionseffektiviteten och produktkvaliteten utan ger också företag mer exakta marknadsprognoser och beslutsstöd.
I framtiden kommer waferskärningstekniken att göra anmärkningsvärda framsteg vad gäller precision, effektivitet och kostnad. Dessa framsteg kommer att driva den fortsatta utvecklingen av halvledarindustrin och ge fler tekniska innovationer och bekvämligheter till det mänskliga samhället.
Publiceringstid: 19 november 2024